We are proud to announce this release, which focuses on time savings on the workshop floor, as well as for the drafters.
These are the new features in Parabuild version 6 :
New match lines capability for DXF and Dstv + contours update
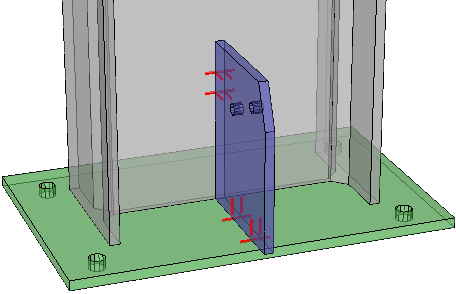
The following new capabilities and updates were done to both DXF and Dstv commands :
- Scribing of contours has been updated with more capabilities such as choosing different scribing on main parts than on subparts, only scribe outer extent corners to minimize the number of corners, and choosing punch marks instead of scribing of full lines or corners.
- In addition to the scribing of sub-part contours, now hole matching lines can also be automatically scribed. The hole axis is projected, and here both the main member and the sub-part can be marked with a short line or a punch mark. Those matching lines/marks can then be simply matched up in the shop to position the parts on the assembly.
- Filters and structural parts can be used to configure which situations should get certain types of scribing. This allows for great user control in the fully automatic scribing system. For example, the user could specify that main members get only punch marks to save time on the beamline, but plates get corner contours with hole match lines for clarity. Another example: a different type of sub-part could get a different style of contour scribing on the main part.
These capabilities will offer the draftsperson and the workshop the following advantages :
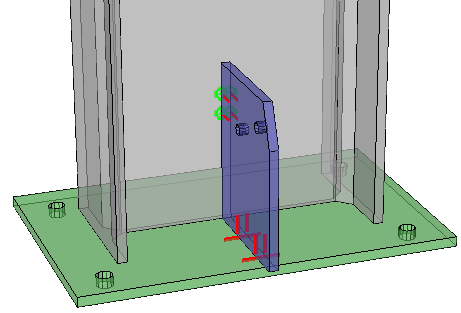
- These advanced scribing options replace the manual scratching/marking when laying out the steel, saving significant man-hours in the shop.
- Contours, punch marks, and hole matching lines are generated directly from the 3D model and can reduce mistakes on the shop floor.
- The capability to use punch marks on some types of parts coupled with scribing on other types can save time on the beamline by using punch marks there, while still having the option to use full or corner contours and scribed hole matching lines on plates.
- Scribing contour and/or part numbers can be skipped entirely for specified situations. This offers further opportunities for optimizing the utilization of the machines in the shop.
- Automatic scribing options can be configured based on the type of part. These settings only need to be configured once, and after that CNC files for the whole model can be generated automatically. This will save the draftsperson time in not having to do changes manually.
All together these features will increase the productivity of the drafters, shop floor staff, and machines in the shop.
Here are some more examples of what is possible with contours and match lines in different situations.
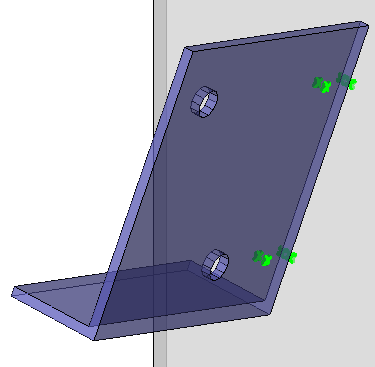
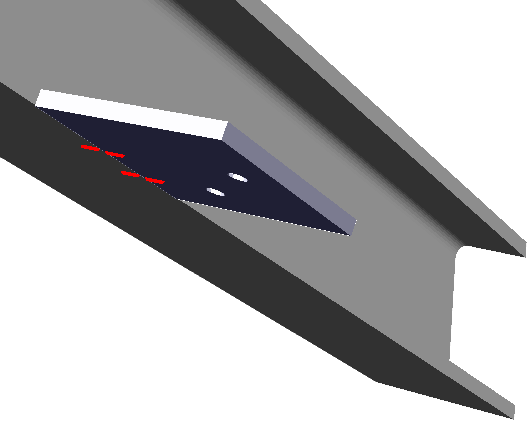
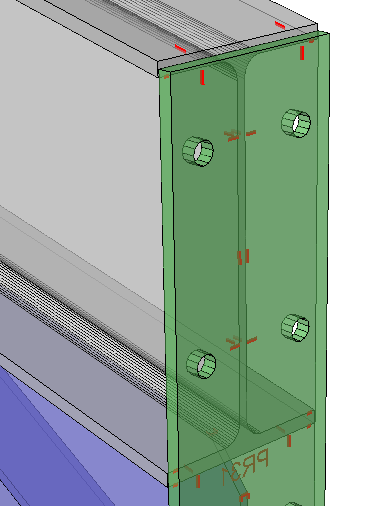
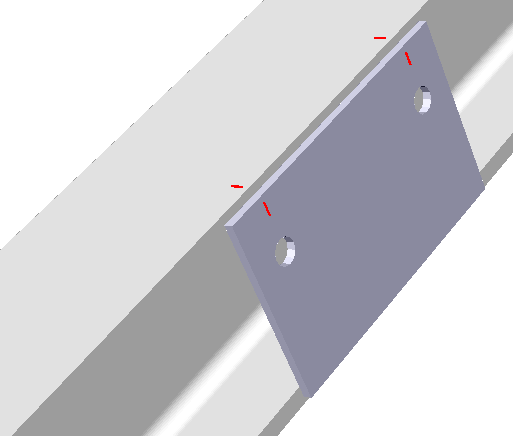
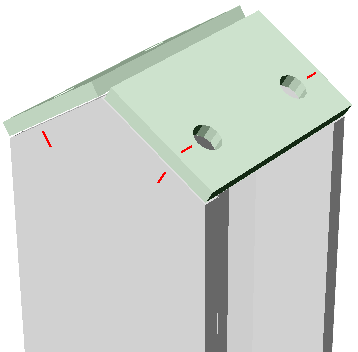
Structural types
The purpose of structural types is to assign type names to parts and assemblies so that those types can be used to automatically assign properties, define behavior specific to that type, or select objects based on their type.
The most obvious examples of structural types are columns and beams.
During or after the structural types are assigned to parts, we can use several tools on these parts, such as :
- Automatically assigning properties to the part. For example, assigning numbering prefix B for Beams and C for columns.
- Automatic selection of all the parts with a particular structural type
- Define a CNC scribing style specific to a structural type
- In the near future, many more applications for structural types will be implemented
Filters
The purpose of filters is to identify specific objects in the model based on a set of rules..
The structural types rely on these filters to classify objects, but that is not the only use case for filters.
Filters can also be used in general to find certain types of parts.
The CNC contour settings for example also use filters to assign different contour options to the type of part.
Filters can use the part properties and even geometrical traits as a condition for passing the filter.
In the near future, many more applications for filters will be implemented
New DSTV options
The following new capabilities were added to the Dstv export :
- Export wraparound-style plate for pipe/CHS to DSTV files
- Automatically add fillets to notches, or replace cuts/notches with drill holes (highly configurable)
- A new option that filters out small planar cuts using a tolerance. Thanks to this option, the machine will not block on double saw cuts on one end of the profile if one of the cuts is negligible.
Dstv Cuts / Notches
Consider the following Dstv end-results that are generated automatically from the same 3D model:
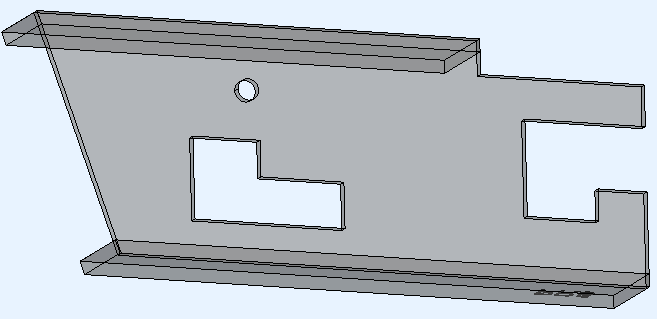
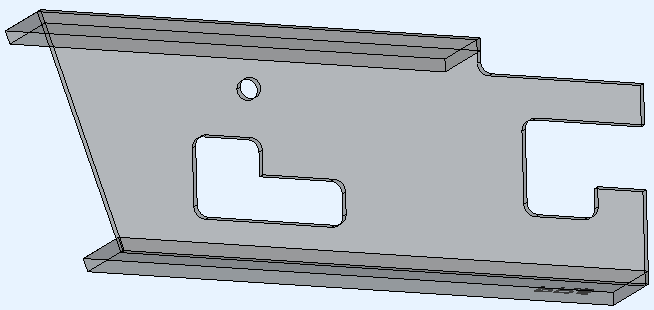
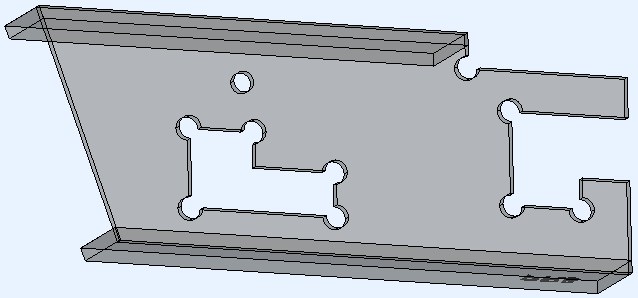
Floating network licenses
A floating Parabuild license can easily move from one user to another user over the internet. The floating license is only available for Full versions of Parabuild and comes at an additional cost.
In Parabuild, a floating network license does not require the installation of a network server.
This service is provided by Parabuild directly over the internet.
Feeding excel values to Macros and arrays
This command can be used to feed cell values from an excel file directly into macros and arrays in a Parabuild drawing.
A mapping file can be used to reduce the need for having to repetitively enter names, but the mapping file is not a requirement.
|
|
In this example the excel file(s) changed the roof height, enlarged the structure, changed the number of portal frames, modified the side rails and did changes to the apex and haunch connections.
Dark theme
Dark theme is now supported for the ribbon and toolbars.
With a special thank you to Theo Brock & son for their help.
New Materials table
This table is used by Parabuild to find out what the weight factor of the materials are.
It also allows us to automatically assign certain properties at the time when a material is assigned to a part.
Each row in the table represents a material.
The grade is combined with the material, that is why we have several different entries for steel in this table.
Curved railings
The macro and array system in Parabuild have been expanded to support curved railings.
A curved railing can be drawn with the regular Railing command, by selecting an arc or an edged of a curved profile.
Macros that use a planar surface now also support other surface types
This new feature applies to all macros that use a planar surface.
When Parabuild prompts you to select the planar surface, you can also select a cylindrical or spherical surface.
While the macro is created, the tool will first calculate the intersection between the profile and the sphere.
Then, the planar surface is calculated by making it tangent to the sphere. This planar surface is then used by the macro to position the parts.
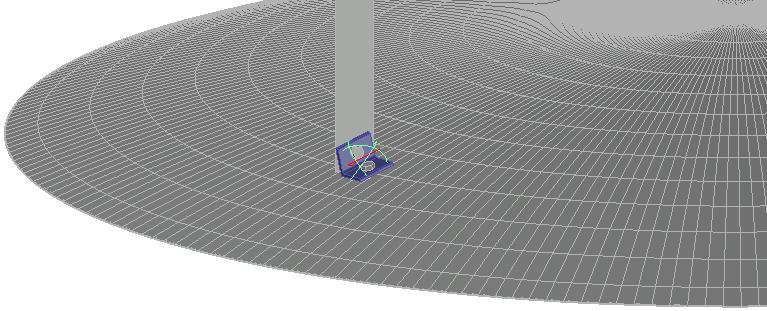
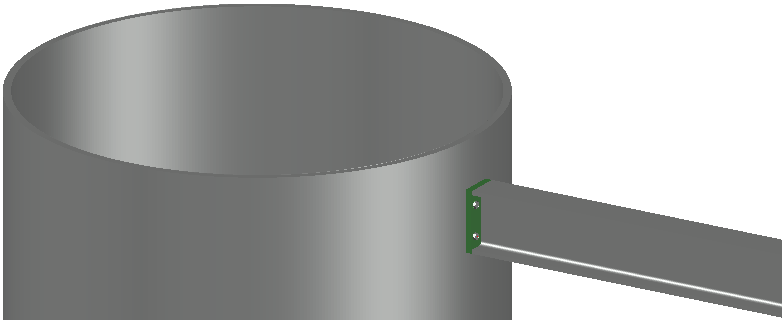
Behavior change to double-clicking parts and macros
When double-clicking a macro or a part, the corresponding macro will be opened in the Review Macro dialog box.
However, pressing the SHIFT and/or CTRL keys while double-clicking will determine the behavior of the action.
These are all the different behaviors, with an example drawing of what would happen when double-clicking a side rail :
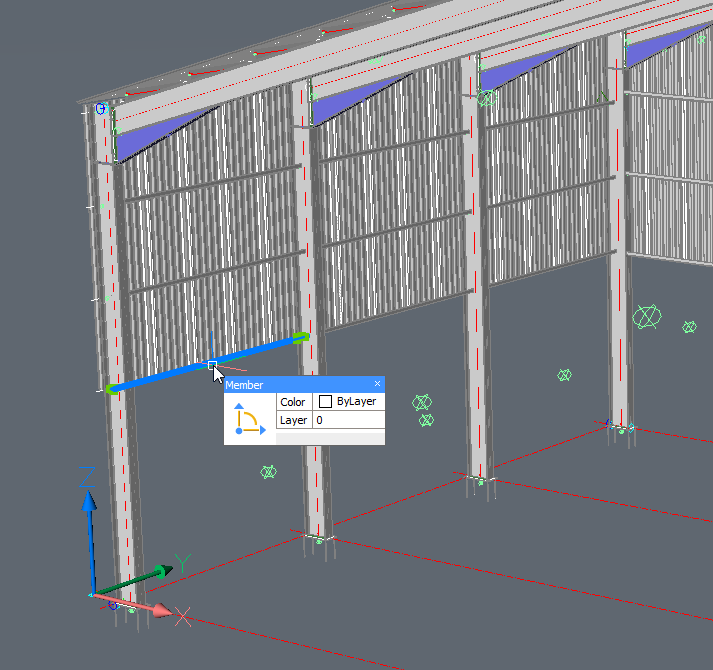
- Double-click without SHIFT nor CTRL pressed – Only the macro of the selected part will be reviewed. In the example, just the macro of the single side rail will be reviewed.
- Double-click with SHIFT OR CTRL pressed – All of the parts that are dependent on the same array will be reviewed. In the example the 4 side rails and the array itself will be reviewed.
- Double-click with SHIFT AND CTRL pressed – The top owning macro of the part that you selected will be opened, together with all of its sub-macros. In the example, the top owning macro is the portal frames macro so the entire drawing will be reviewed. That is because the entire drawing is fully parameterized.
New option for adding position details on the assembly drawing
The assembly shop drawing generation now has a new option for adding all of the position details on the shop drawing.
This will of course result in a larger drawing, but there is also the possibility to skip the position details of the main part.
All of the main part’s dimensions can also be activated on the views of the assembly itself so that all of the information for fabrication is still there on the sheet in case you would use this last option.
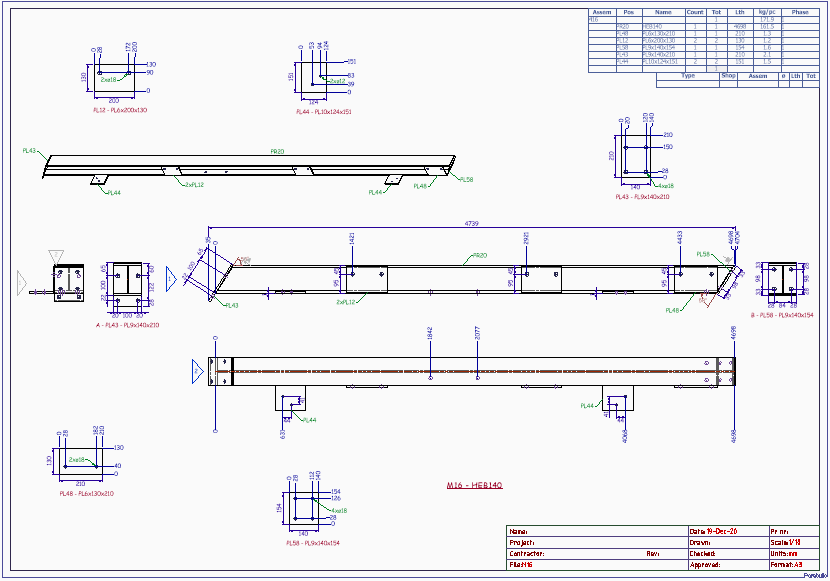
New view option for shop drawings : annotate the isometric view
Adding the annotations to the isometric view will help with more quickly identifying parts of the assembly.
New view option for views : do not show lines occluded by the part itself
By activating this, many of the hidden lines are cleared, uncluttering the view.
To illustrate the differences, here are examples of the 3 different hidden line options that are available :
|
|
|
|
|
With the hidden lines option active, we can see the part behind the column.
With the occluded by self option active, most of the clutter of invisible lines will be cleared while still keeping hidden parts visible.
This option will be very useful for the 3D isometric view on shop drawings.
The new hidden line method will help clarify the assembly’s composition.
New option for automatic tags : sticky tags
Sticky tags are tags that will stick to the edge of the annotated part, so that a leader is not necessary.
When activated, Parabuild will automatically decide for each tag whether to make it sticky or not. A tag will only become sticky if the part has an edge that is long enough for the tag to stick to, without intersecting any other lines.
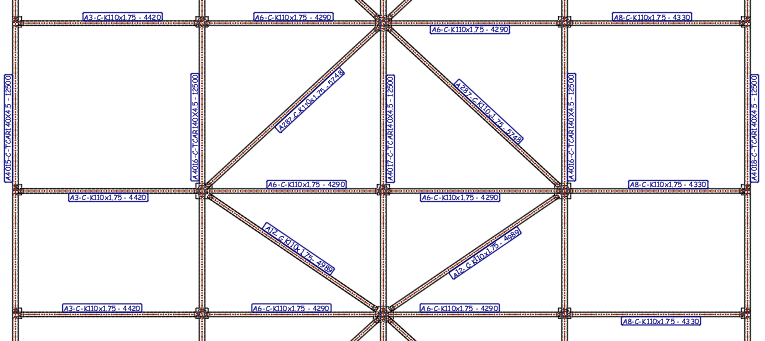
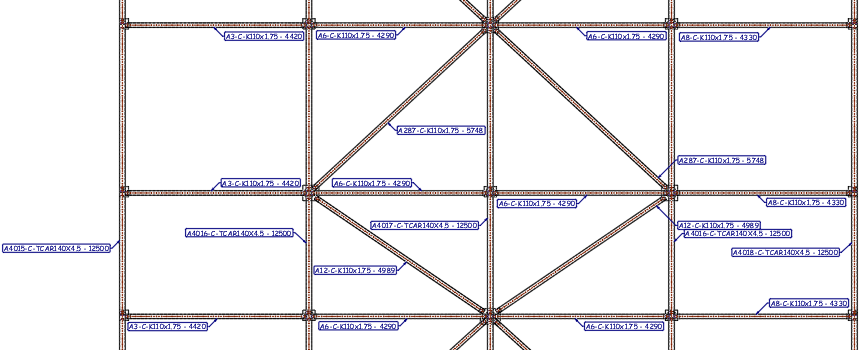
New options for the relation between the thread and the shear plane of bolts
The bolt assemblies have the following new options :
These options allow you to choose the location of the thread end, at one of these 3 locations :
|
|
|
|
|
|
New bolt property : number of filler washers
When the Filler washers (Packing washers) option of the bolt is enabled, and the shank of the bolt extends beyond the Grip (see illustration), then Parabuild will automatically add as many washers as necessary to make sure that the nut does not touch the thread runout or shank.
This property shows the number of filler washers that were applied on this bolt for this purpose.
New bolt property : Do not drill filters
With this property, it is possible to have the bolt not add any holes to certain objects
This is done with the help of multiple filters that can be entered per bolt.
To learn more about these new features and how to use them, see the Release notes for version 6.